Boston
12MWe Biomass Project
Executive Summary
Objectives
Our aim is to create a Green Energy Generator and Supply Company, with operational recycling, energy from waste and lightweight aggregate production EcoParks located on sewage treatment works (STW) and other sites close to all the major conurbation centres around the UK. Further, to design and develop turnkey power projects on behalf of clients such as Mick George Ltd.
We currently have 10 project sites, 8 of which are on sewage treatment works (STW) these sites will become EcoParks housing three totally different but complimentary technologies, sites 9&10 being the Boston Project 1&2 (which is the primary object of this document) each will house a single technology (Gasification plus ACT).
The 8 main STW sites, each designed, generating 154,000MW/hrs exportable (net), produce 200,000 tonnes of high quality lightweight aggregates (can be to specification), divert 300,000 tonnes of MSW from landfill, utilise 70,000 tonnes of sewage sludge in aggregate production, and produce 308,000 ROCs. (EcoParks will be described later in this documents under the heading “EcoParks Rollout”).
The Company intends to achieve outstanding financial performance by virtue of the effect of landfill tax on waste gate fees combined with the exceptionally high government incentives offered to stimulate investment in this form of Green Energy. These measures interact with diminishing landfill capacity to give the venture a guaranteed, recession proof, high level profitability for the foreseeable future.
The initial objective is to be operational with the first 2 plants (Boston 1&2) on a 2 year timescale and thereafter bring 8 new plants into service at the rate of two per year. The financial objective is to achieve an EBITDA in excess of £450m by 2016.
Mission Statement
The generation of revenue and profit, by replacing significant levels of fossil fuel generation, with clean, sophisticated energy production, in plants which divert waste streams from landfill and help recycle our scarce resources.
Technology
First, it’s important to convey the R&D effort put in to establishing the EfW system we have today. Over 10 years of R&D, we tested every waste stream and assessed every kind of thermal unit; thermal reclamation units, step grate boilers, twin stage boilers, fluidised bed boilers (FB), gasifier, FB gasifier, FB steam reforming gasifier, FB staged gasifier, down draft gasifier, low & high temp pyrolysis, pyrolysis/gasification, gasification/plasma, plasma conversion, etc. Whilst all thermal technologies (with the exception of plasma conversion) come under the waste incineration directive, its only the actual flame producing systems such as twin stage wood burning boilers, step grate boilers and alike that can be likened to incinerators.
Gasification combined with Plasma (Gasplasma) or Plasma Conversion are systems that are undoubtedly the cleanest systems of all, but unfortunately the down side is, the systems carry high maintenance cost, relatively low operating hours and exceptionally high parasitic power usage. (8.5MWe = 5.5 exportable) therefore making the systems unviable.
Pyrolysis/Gasification: there are many small scale (up to 50kg/hr) test plants across the world but no one has managed to scale up to commercial status. Pyrolysis: there are many small scale (up to 50kg/hr) test plants across the world but again, no one has managed to scale up to commercial status. However, several years ago in the UK, there was a DTI funded 0.5t/hr plant at Welsh Water that operated for just short of a year, fuelled by dried sewage sludge pellets. The unit, designed by Waste Gas Technology Ltd was forced to close after an accident in the drying process.
AUG believes the best available EfW systems today are fluidised bed Gasifier’s, the best type however, is a steam reformation system as it produces Hydrogen rich Syngas (c. 40% Hydrogen) which would fuel down rated gas engines. However, AUG has the technology to enable small to medium sized Gas Turbines to run on relatively low CV and/or Hydrogen rich Syngas, our turbines would run in combined cycle giving far greater efficiency (50-55%) [Steam turbine 30-32% & IGCC 50-55% efficiency] .
Unfortunately, the only steam reformation unit operating, is in Austria and there are no commercial reference sites (Yet) and until there are, the best system is the more robust fluidised bed Staged Gasifier, where the Syngas is combusted within its second stage and steam is raised by an in line heat recovery steam generator (HRSG). This system generates power via Steam Turbine only.
Our choice is Energy Products of Idaho (EPI) Fluidised Bed Gasification Technology. EPI have reference plants in several countries and Funder's can see that we have as far as possible removed technology risk (ref Plant list Appendix H). The EPI Staged Gasifier was initially chosen as best available technology, however, in a meeting at Ofgem with David Fletcher, (Ofgem’s author of the final guidance on ROC banding) AUG was able to present both EPI Gasifier’s in relation to the Boston project, Ofgem referred to the difficulty in defining the point where PGS (Power Generation System) begins, “where is the line drawn?” we can see from Fig.1, although it shows the green syngas sampling port, it’s difficult to draw the line where Syngas production ends and PGS begins. However, with Fig.2, there is no doubt, the Syngas produced will leave the Gasifier and be tested under Ofgem conditions prior to being combusted via a specially designed burner (boiler). AUG have therefore taken Ofgem’s advice and selected the EPI straight Gasifier for Boston.
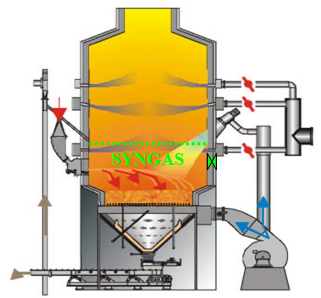 |
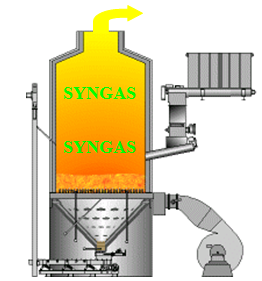 |
Figure 1: Staged Fluidised Bed Gasifier |
Figure 2: Fluidised Bed Gasifier |
|